Un nuovo report elaborato dalla International Energy Agency e dallo European Patent Office offre una panoramica molto interessante su quella che è l’attività brevettuale nell’industria dell’idrogeno nel mondo. La ricerca e l’innovazione tecnologica sull’idrogeno come vettore di energia pulita è un tassello fondamentale per la transizione energetica, nel passaggio a forme di energia sostenibile e rinnovabile per il futuro dell’economia mondiale.
Una prospettiva in cui anche Tempco crede molto, lavorando allo sviluppo di soluzioni tecnologiche innovative ad esempio nel comparto navale per una navigazione a zero emissioni e per la produzione di idrogeno e alimentazione mediante elettrolisi, grazie all’impiego degli innovativi scambiatori PCHE.
Lo studio rileva quindi che l’innovazione nell’industria dell’idrogeno è molto attiva in una varietà di ambiti: dalla produzione per elettrolisi dell’acqua allo sviluppo di serbatoi in grafene, dalla tecnologia delle celle a combustibile nel trasporto aereo e non solo allo stoccaggio criogenico dell’idrogeno, e fino alla riduzione del minerale di ferro.
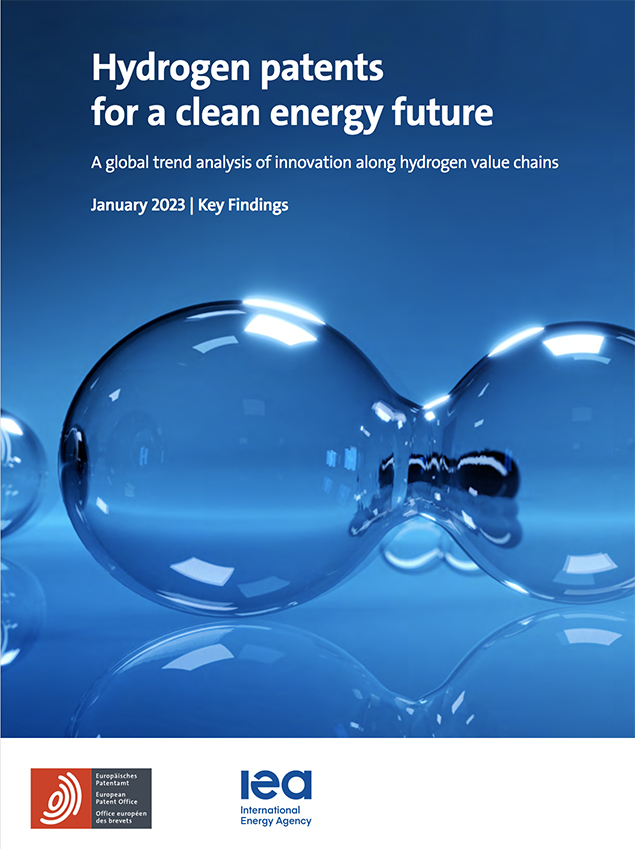
L’indagine copre tutte e tre le principali aree dell’industria dell’idrogeno, ovvero produzione e approvvigionamento, stoccaggio, distribuzione e trasformazione dell’idrogeno e applicazioni finali. Nel periodo 2011-2020 circa la metà delle famiglie di brevetti internazionali (IPF) era legata alla produzione di idrogeno, mentre gli altri IPF erano divisi tra applicazioni finali dell’idrogeno e tecnologie per il suo stoccaggio, distribuzione e trasformazione. A guidare le attività per numero di brevetti è l’Europa, con il 28% di tutti gli IPF nel periodo considerato, con vantaggi tecnologici trasversali a tutti e tre i segmenti della catena del valore dell’idrogeno, con l’11% dei brevetti depositati in Germania e il 6% in Francia. Secondo è il Giappone, con il 24% dei brevetti, seguito dagli Stati Uniti, che hanno contribuito per il 20% dei brevetti pubblicati. Mentre però Europa e Giappone hanno registrato un incremento annuo rispettivamente del 6,2% e del 4,5% nel decennio, gli Stati Uniti sono l’unico Paese ad aver avuto un rallentamento. Ancora poco rilevante l’attività brevettuale in Corea e Cina, che hanno però mostrato i tassi di incremento maggiori, con crescita annue medie del 12,2% e del 15,2% rispettivamente, con una forte focalizzazione sulle tecnologie emergenti per applicazioni finali dell’idrogeno nel caso della Corea.
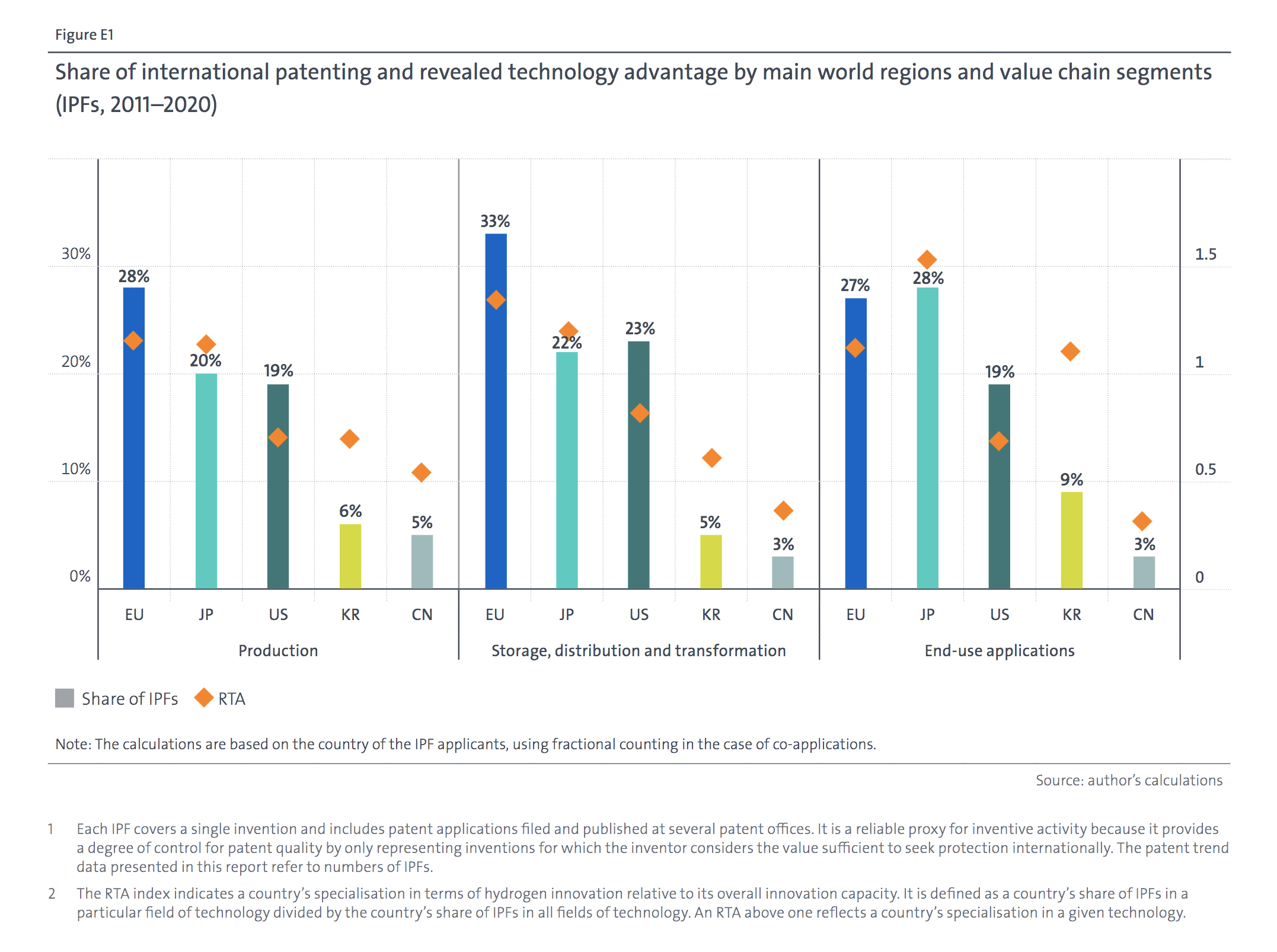
Il report opera inoltre una distinzione tra l’attività brevettuale correlata al miglioramento di tecnologie già esistenti e quella legata a tecnologie emergenti che puntano a utilizzare l’idrogeno come fonte alternativa contro il cambiamento climatico. Le innovazioni nelle tecnologie già esistenti provengono per la maggioranza da industrie nel settore chimico, concentrandosi sulla produzione e gestione dell’idrogeno, con diversificazione su tecnologie emergenti di carbon capture usage & storage (CCUS). Tra le più attive, figurano i nomi di Air Liquide, Linde, Air Products e BASF. I brevetti in tecnologie emergenti legate alla transizione energetica sono invece a opera soprattutto di società in ambito automotive, con nomi quali Toyota, Hyundai, Honda e Panasonic, concentrate in particolare sulla produzione di idrogeno per elettrolisi e applicazioni finali tramite celle a combustibile.