Supermicro, produttore di server per high performance computing per applicazioni in data center, cloud computing, AI, 5G e edge computing, ha dimostrato in concreto i vantaggi che è possibile ottenere con il raffreddamento a liquido per immersione in fluidi dielettrici dei dispositivi elettronici. L’azienda ha infatti condotto dei test sul raffreddamento per immersione in collaborazione con 3M, Intel, Kaori e Samsung misurando non solo la superiore efficienza di raffreddamento ottenibile, con riduzione del consumo energetico, ma anche i risparmi nei costi relativi alle licenze d’uso dei software EDA (electronic design automation) impiegati nell’industria dei semiconduttori.
Il raffreddamento a liquido per immersione, di cui abbiamo già parlato in passato mediante utilizzo di scambiatori TCOIL, aumenta in prima istanza la sostenibilità dei data center, migliorando l’efficienza energetica del sistema di raffreddamento. Infatti, utilizzare un liquido come fluido di raffreddamento invece dell’aria comporta un contatto più stretto delle particelle del liquido con l’oggetto da raffreddare, aumentando il coefficiente di scambio termico. Questo consente inoltre di utilizzare fluidi di raffreddamento a temperature meno spinte, con notevole risparmio energetico grazie anche alla possibilità di impiegare sistemi in free cooling per il raffreddamento dei fluidi dielettrici e tagliando i costi legati al condizionamento dell’aria.
La soluzione con raffreddamento a liquido nel progetto testato ha però altresì portato a una riduzione dei costi di esercizio del calcolo ad alte prestazioni richiesto dai software EDA, dove il costo delle licenze d’uso è legato al numero di core e alla frequenza di Clock richiesta (la frequenza di Clock indica il numero di cicli da acceso-spento, ossia tra 0 e 1, che un transistor è in grado di processare in un secondo, misurata in GHz). Grandezze a cui è legato anche il TDP (thermal design point), ovvero il calore massimo che un processore deve smaltire per funzionare in maniera ottimale.

Il costo complessivo delle licenze può quindi essere ridotto diminuendo il numero di core utilizzati e aumentando la frequenza di clock, ottenendo lo stesso livello di prestazioni. Ciò comporta però un incremento nella quantità di calore sviluppato dall’elettronica da dissipare, che mette le soluzioni di raffreddamento ad aria tradizionali di fronte al loro limite, potendo invece essere gestite senza problemi e con maggior efficienza e consumi inferiori dal raffreddamento a liquido per immersione.
Il sistema prototipale messo a punto da Supermicro in collaborazione con 3M, Intel, Kaori e Samsung sfrutta nello specifico il raffreddamento a immersione diretta di due tipologie di dispositivi di Intel e Samsung, in un serbatoio con sistema a scambiatori di calore a piastre riempito con il fluido 3M Fluorinert Electronic Liquid FC-40, che ha mostrato perfetta compatibilità con l’elettronica impiegata.
I test condotti hanno dimostrato una importante riduzione del consumo energetico ottenuta con il raffreddamento a liquido per immersione, anche con CPU ad alte prestazioni e in ambienti a temperatura ambiente, senza impiego di aria condizionata. Consentendo la riduzione del numero di core nei processori e l’incremento della clock speed. Prospettando pertanto il raffreddamento a liquido per immersione come una soluzione green e altamente efficiente in grado di ridurre anche i costi di esercizio, adatta alle crescenti potenze di calcolo richieste ai data center a sostegno dello sviluppo delle nuove tecnologie, dal campo della progettazione elettronica, all’intelligenza artificiale e all’analisi dei dati.
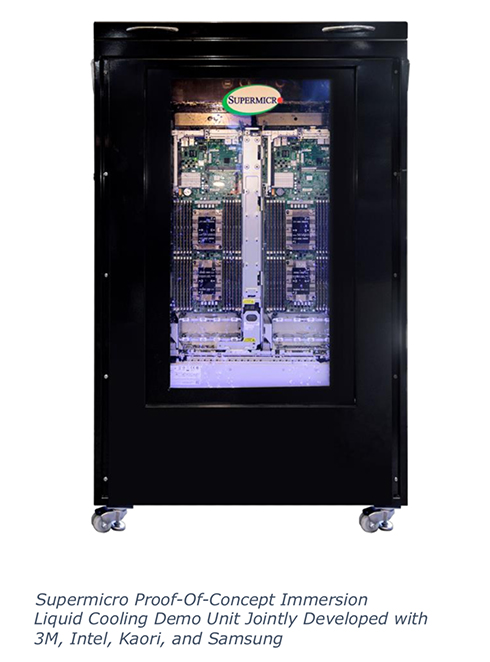
Source: Supermicro
Per restare informato ogni mese sulle ultime applicazioni di gestione dell’energia termica, iscriviti alla Newsletter – Solid Temperature di Tempco.