A new report by the International Energy Agency and the European Patent Office offers a very interesting overview of patent activity on hydrogen industry in the world. Research and technological innovation on hydrogen as a clean energy carrier is a fundamental piece on the path to energy transition, in search of sustainable and renewable forms of energy for the future of the world economy. A perspective in which Tempco is also very much committed, working to develop innovative technological solutions for example in the marine sector, for zero emission yachting, as well as in hydrogen production and fuel systems though electrolysis, thanks to the use of innovative PCHE exchangers.
The study therefore finds that innovation in the hydrogen industry is very active in a variety of areas, from the production by electrolysis of water to the development of graphene tanks, from fuel cell technology in aircraft motors and beyond to cryogenic storage of hydrogen, and up to the reduction of iron ore.
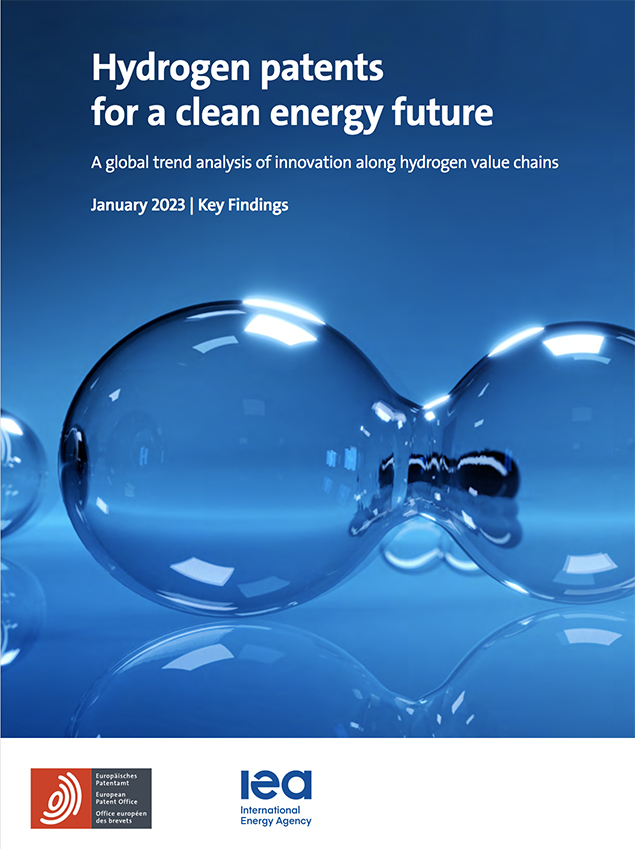
The report covers all three main areas of the hydrogen industry, namely hydrogen production and supply, storage, distribution and transformation, and final applications. In the period 2011-2020, approximately half of the international patent families (IPFs) were linked to the production of hydrogen, while the other IPFs were divided between final applications of hydrogen and technologies for its storage, distribution and transformation. Leading the activities by number of patents is Europe, with 28% of all IPFs in the period considered, with technological advantages transversal to all three segments of the hydrogen value chain, with 11% of patents deposited in Germany and 6% in France. Second is Japan, with 24% of patents, followed by the United States, which contributed 20% of published patents. However, while Europe and Japan recorded an annual average increase of 6.2% and 4.5% respectively over the decade, the United States is the only country to have recorded a slowdown. Patent activity in Korea and China is still not very significant, but they have shown the highest growth rates, with average annual growth of 12.2% and 15.2% respectively, with a strong focus on emerging end-use technologies of hydrogen in the case of Korea.
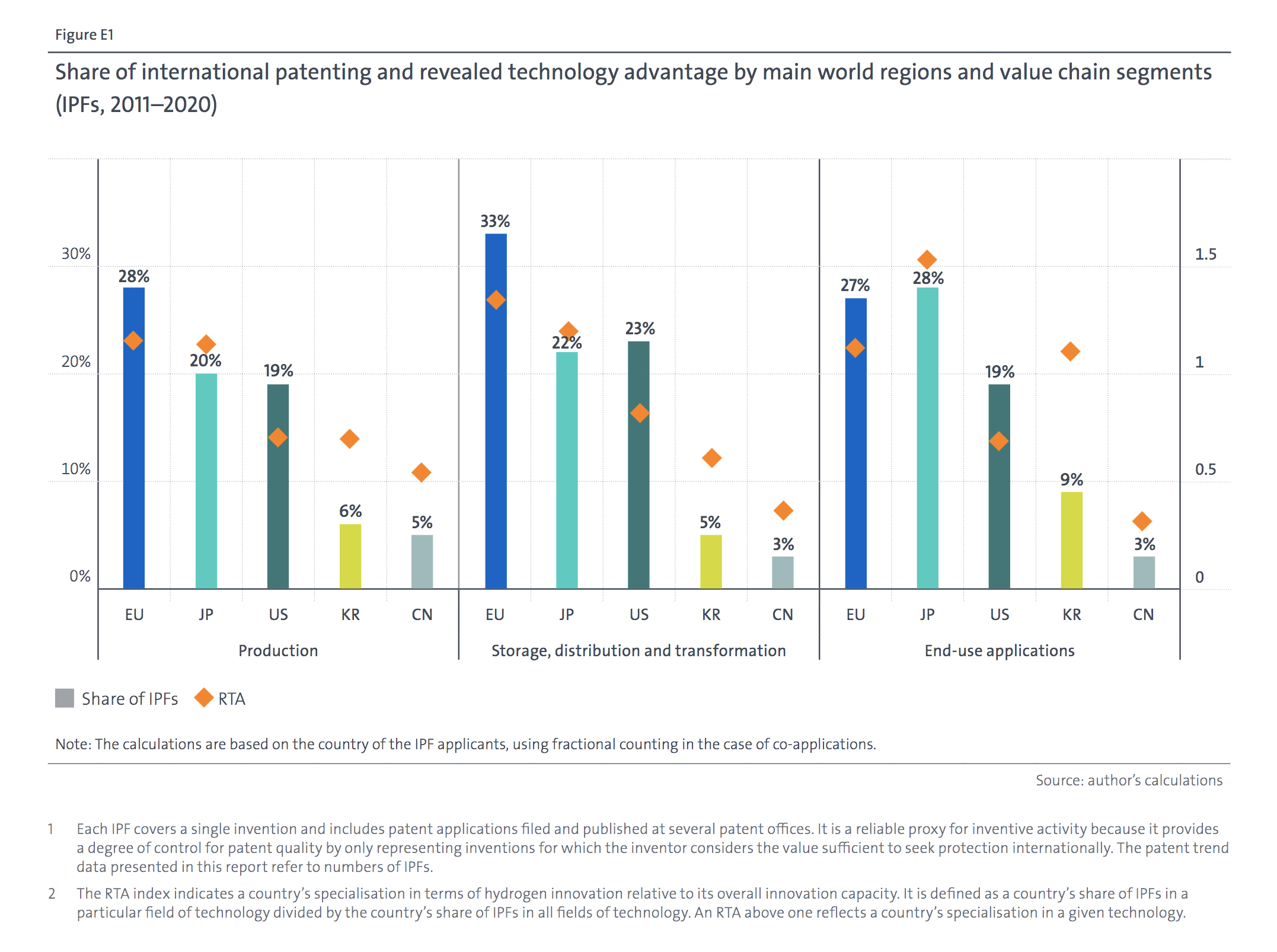
The report also makes a distinction between patent activity related to the improvement of already existing technologies and that related to emerging technologies that aim to use hydrogen as an alternative source against climate change. Innovations in existing technologies came mostly from industries in the chemical sector, focusing on the production and management of hydrogen, with diversification into emerging carbon capture usage & storage (CCUS) technologies. Among the most active, there are companies such as Air Liquide, Linde, Air Products and BASFPatents in emerging technologies linked to the energy transition are mainly coming from companies in the automotive sector, with companies such as Toyota, Hyundai, Honda and Panasonic, focused above all on the production of hydrogen by electrolysis and final applications using fuel cells.