Current rectifiers are essential components in modern electrical systems, responsible for converting alternating current (AC) to direct current (DC). However, the process can generate excess heat that must be dissipated in order to maintain their efficiency and reliability.
Generally, air cooling is the most common solution to dissipate the heat generated by power rectifiers. This method uses the principle of heat transfer through direct contact with ambient air. In this case, fans and heat sinks are key components. The fans draw in ambient air, which passes through the heat sinks, thus removing excess heat generated by the rectifier.
An air cooling system entails both advantages and disadvantages. The advantages of air cooling are:
- Economical: air cooling systems are generally cheaper to implement than water-based ones.
- Simple maintenance: maintenance of air systems is often easier, since it does not involve liquids and complex piping.
On the other hand, air cooling has these disadvantages:
- Efficiency limit: air cooling systems can reach an efficiency limit under heavy load situations, limiting their ability to dissipate large amounts of heat.
- Noise levels: fans can produce noise, which may be an undesirable factor in noise-sensitive environments.
A valid alternative for dissipating the heat generated by rectifiers therefore consists of water cooling. This is a more advanced technology that uses liquid coolant to absorb and transfer heat away from power rectifiers. This method involves a piping system, a pump and radiator that allow liquid to circulate through the system, cooling the rectifier.
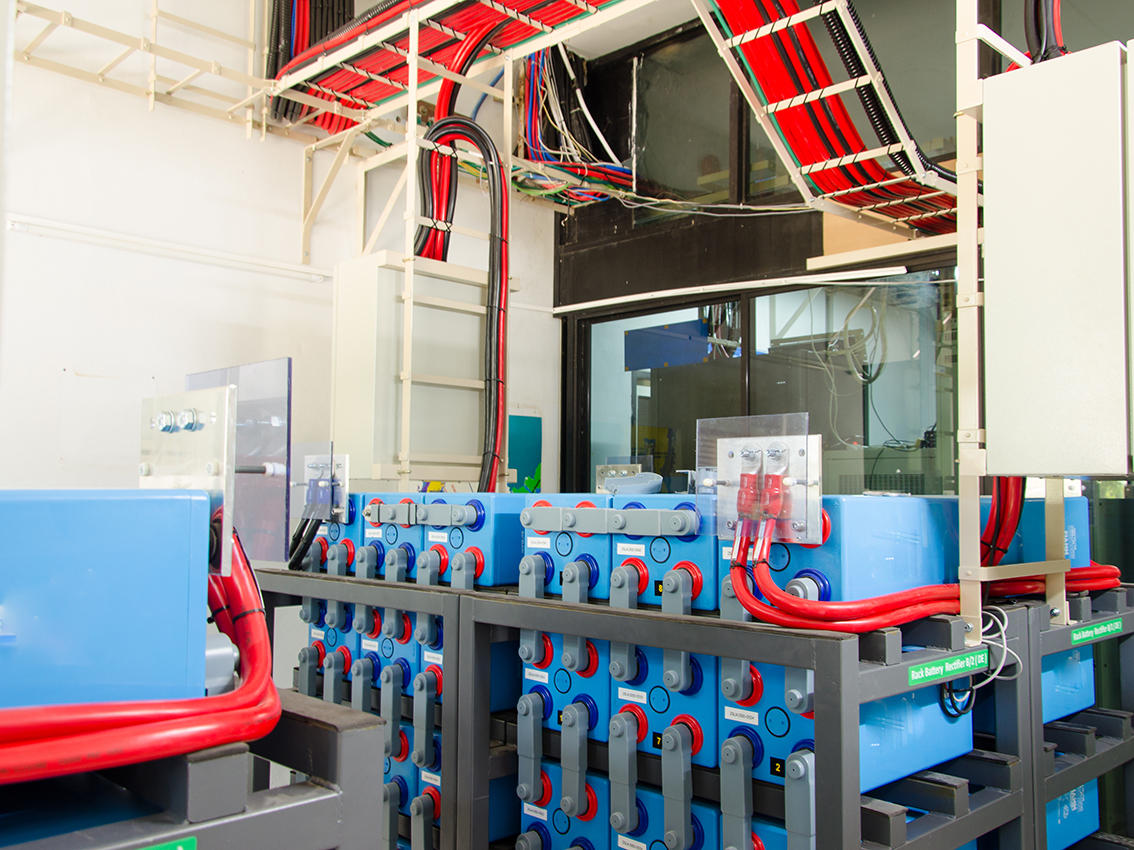
Advantages of water cooling:
- High efficiency: water cooling is generally more efficient than air cooling, allowing to handle more intense workloads.
- Quiet operations: unlike fans, water cooling can be noticeably quieter, providing an ideal solution for noise-sensitive environments.
The disadvantages of water cooling are the following:
- Expensive: implementing water cooling systems is usually more expensive due to the complexity of the components involved.
- Complex maintenance: water systems require more careful and periodic maintenance, especially to prevent problems related to corrosion and liquid leaks.
In fact, the choice between air and water cooling for power rectifiers therefore depends on various factors, including the operating environment, the power capacity of the system and the available budget. While air cooling offers an economical and easy-to-maintain approach, water cooling stands out for its high efficiency, especially in labor-intensive and demanding environments. Ultimately, the decision will depend on the specific needs of the electricity system involved.
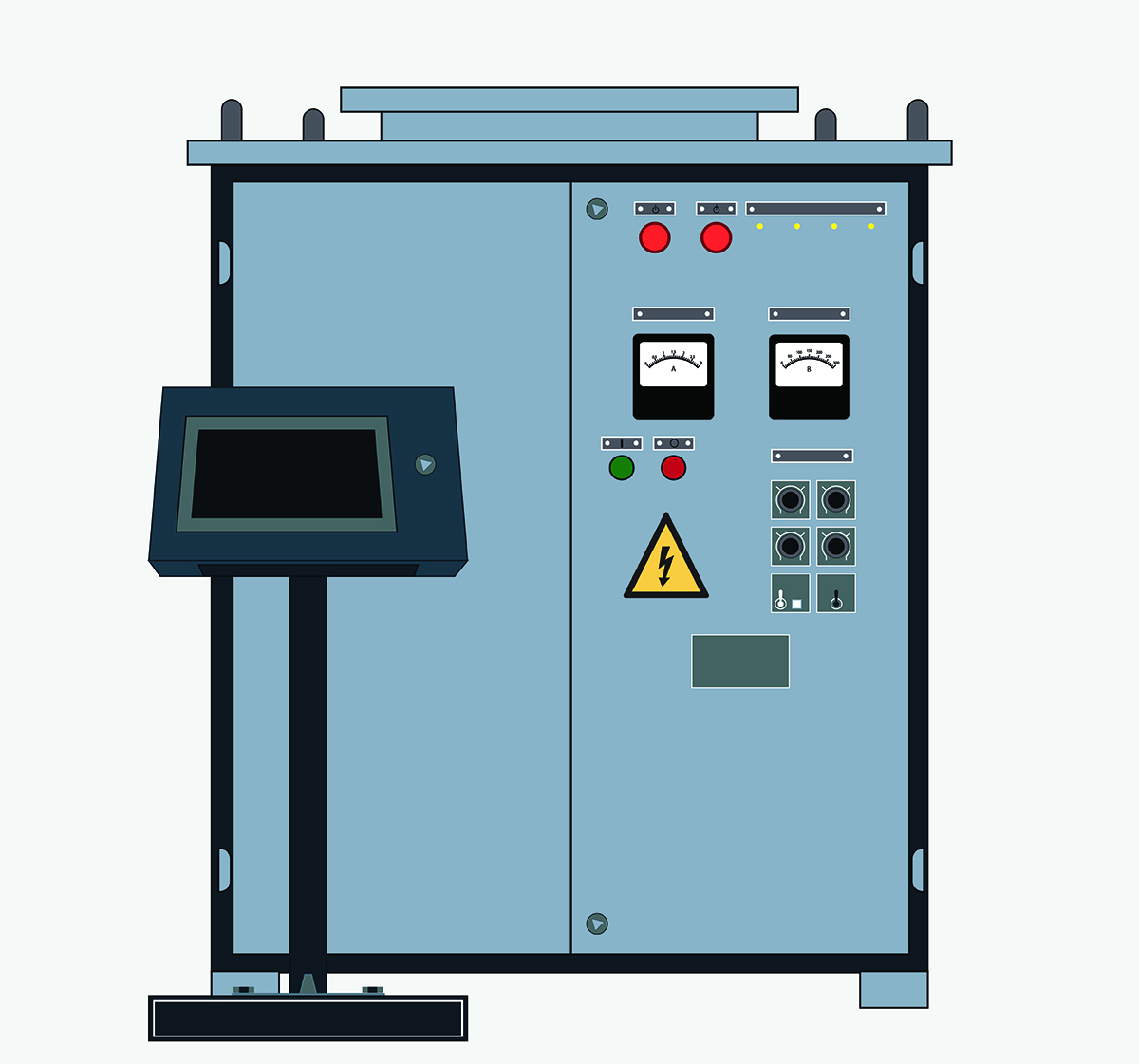
In case of water cooling, by placing an exchanger with a dedicated system, maintenance problems due to limescale are eliminated. An interesting application here is related to the modern needs of hydrogen production systems through electrolysis.