In terms of heat transfer and thermoregulation, dimple jacket exchangers can be a very efficient and versatile solution, because of their construction and thermal transfer efficiency.
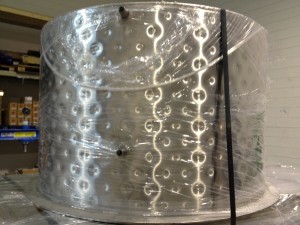
Dimple jacket exchangers
T COIL dimple jacket exchangers are plate heat exchangers made by inflating through high pressure two welded metal sheets, in order to create a chamber with special cavities and channels for the flowing of the fluids, achieving uniform heat exchange. The peculiar design engineering and the way of construction allow to use this kind of heat exchangers for clamp-on applications, on tanks and vessels intended for working and process fluids thermoregulation.
Dimple jacket heat exchangers are also in addition a very efficient and suitable solution for immersion coil application in heating and cooling purposes, for prime heat exchange by direct contact with the fluids in thermoregulation.
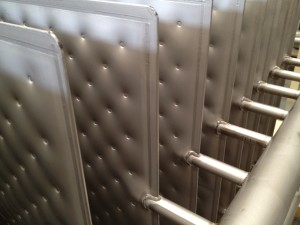
Heat exchangers
Both external or internal applications are indeed possible, and in case of clamp-on external design, many shapes and customized sizes can be realized, also through our plate heat exchangers Tempco online Store, in order to obtain even more versatile thermostatating machines, tailored on any industrial process need.
Maximum construction flexibility makes dimple jacket heat exchangers a perfect application for industrial energy efficiency and thermoregulation in a series of sectors and production processes, such as:
– textile industry
– pharmaceutical industry
– food and dairy
– chemical industry
– paintings plants
– falling film coolers
– fermentation in craft beer brewing
– data center cooling
Applications can vary from in tank fluids thermoregulation with temperature control to cooling and heating, free cooling, heat recovery.
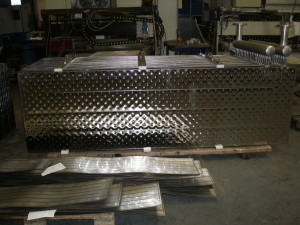
Dimple jacket heat exchangers
Remarkable mechanical resistance, always with PED compliant construction, also allows to employ materials and plates with extremely fine thickness, containing costs and increasing thermal transfer efficiency and heat exchange coefficients.
More articles on this topic:
T COIL on craft beer brewing
T COIL textile industry application