Sometimes I think it is useful to remember that the options to use plate heat exchangers are too great and allow the use in many different applications …
Tempco T PLATE P plate heat exchangers are complete of a support frame in painted carbon steel or stainless steel (for food and diary or pharma applications) and a plate pack with clip gaskets. There are different thermal lenghts, pressing depth and chevron angle.
Standard plates materials
AISI 304, AISI 316, TITANIO, TITANIO/PALLADIO, 254SMO, HASTELLOY C276, INCONEL, MONEL
Standard gasketed material
- NITRIL
- NITRIL PEROXIDE
- EPDM
- EPDM PEROXIDE
- FPM
- PTFE
Gaskets type
LOCK SYSTEM GLUELESS (clip)
STANDARD PLATES RANGE
Connections from DN25 up to DN500 Standard connections:
threaded external or internal UNI and/or BSP, flanged UNI, ANSI, SAE TRICLAMP, for food and diary or pharmaceutical applications
Pressure range from PN6 up to PN25, full vacuum.
Temperature range from -50°C up to +200°C.
FRAMES
Painted carbon steel
Epoxy painting system for marine or aggressive environment
Acid proof painting
Teflon based painting
Special paniting system per food anvironment
Stainless steel multipass for diary applications
Pasteurizer multisection frames
Twin unit
BOLTS
Galvanized carbon steel
Stainless steel sor food and diary executions
SPECIAL EXECUTIONS
Electropolished plates for pharmaceutical applications
Double wall execution, for safe application on pharme, food and diary processes. DW application is a must where the 2 fluids can’t mixed themselves.
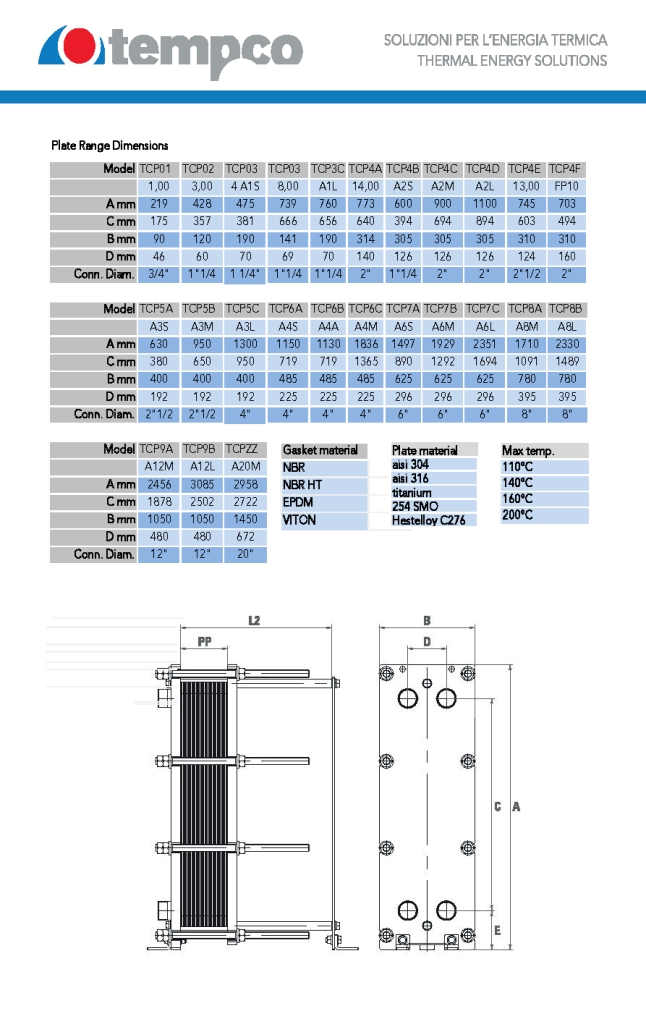