Regulations and policy makers are concentrating the development of the automotive of the future towards electric motors and electrification, but there is another viable alternative solution that would allow to maintain endothermic engines in traditional vehicles: these are the e-fuels, a class of alternative synthetic fuels ensuring carbon neutrality. First of all, e-fuels, also known as electrofuels, are not biofuels, which are obtained from used oils, wastes and biomasses.
The synthetic fuels, or e-fuels, are obtained by extracting hydrogen using electrolysis leveraging renewable energy, therefore through a completely sustainable production process. Hydrogen is then combined with CO2 creating a liquid energy vector. E-fuels are said to be decarbonized because during combustion they produce an amount of CO2 that equals the same amount that gets absorbed while producing them, achieving a circular process at zero impact on the environment, and in fact more sustainable than the production of batteries for electric vehicles.
The most common one is the synthetic fuel, or also synfuel, a mixture of hydrogen and CO2 which is also the basic component of many types of e-fuels. It can power traditional endothermic engines with no emission of sulphur dioxide nor other harmful substances.
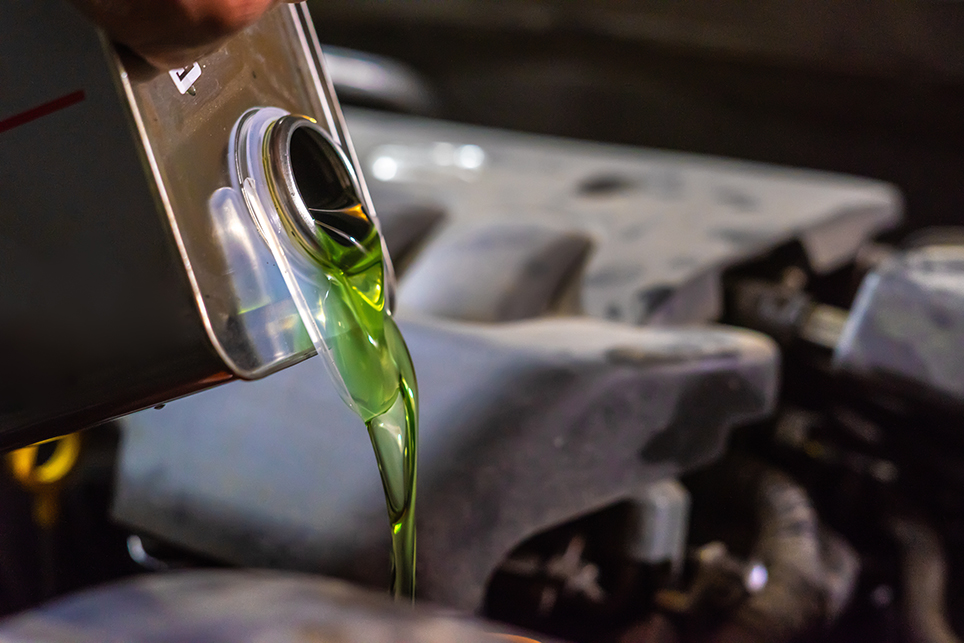
Power to liquids technology is also employed to produce synthetic diesel fuel, or e-diesel, created from carbon dioxide, water and electricity coming from renewable sources, obtaining a liquid energy carrier called blue crude, which is then refined to generate e-diesel. There are also synthetic kerosene, which is already employed in the aviation sector, and synthetic methane, the most simple of all the e-fuels due to the fact that this is not oil-based, its production could be more easier and cheap not requiring refining.
Eventually let’s not forget hydrogen, green hydrogen obtained through electrolysis of water, and blue hydrogen, obtained by splitting natural gas into hydrogen and CO2, in fact using a reverse production process compared to e-fuels production.
It’s then very important to underline once again that e-fuels are compatible with traditional endothermic engines, thus not requiring the shift to electric powertrain. More over, e-fuels are also compatible with existing distribution plants and fuel stations already employed for traditional vehicles. Unfortunately, at the moment the production of these alternative sustainable fuels is still very expensive, but in the next years, with a larger adoption, the prices could lower reaching the same cost of actual traditional fuels.
The eFuel Alliance says that industrial-scale e-fuels production should start in 2025, with a cost that could approximately be about 1.60 euro/l or slightly more. Looking forward, by 2050 the cost could be in the range between 0.70 euro/l and 1.33 euro/l.
Stay updated on the latest applications of thermal energy management by subscribing our monthly Tempco Newsletter – Solid Temperature.