Microchannel Devices, Tempco partner for PCHE exchangers, has finally officially unveiled details related to an important order for the development of a large printed circuit PCHE heat exchanger for use in the oil & gas sector.
The project represents a fundamental milestone, marking the entry of PCHE heat exchangers into applications for the offshore oil & gas sector, in addition to the various solutions already developed in the green energy and renewables sector and in particular hydrogen. After the signing of the contract at the end of last October with Rosetti Marino, for the development and production of a PCHE printed circuit exchanger intended for hydrocarbon sour gas cooling in the new gas recovery module installed on an offshore platform off the coast of Libya, Microchannel Devices is now very pleased to announce the deployment of the project and to share more details about it.
Rosetti Marino is among the most important EPC operators (Engineering, procurement & construction) active in the Oil&Gas sector for oil platforms. The company was looking for a manufacturer of large PCHE exchangers who would be able to create an exchanger compliant with the stringent requirements of the ASME standard for ‘lethal’ gas applications by mid-2025.
The order got underway thanks to the commercial support of Tempco, and the intense work of the MCD team led in a few weeks to defining a PCHE concept capable of satisfying all the requirements posed by the ASME regulation as well as by the end user ENI, by Saipem (main contractor) and RINA (third party inspection body). In this regard, the great support of ICIM‘s ASME representative has been also as precious.
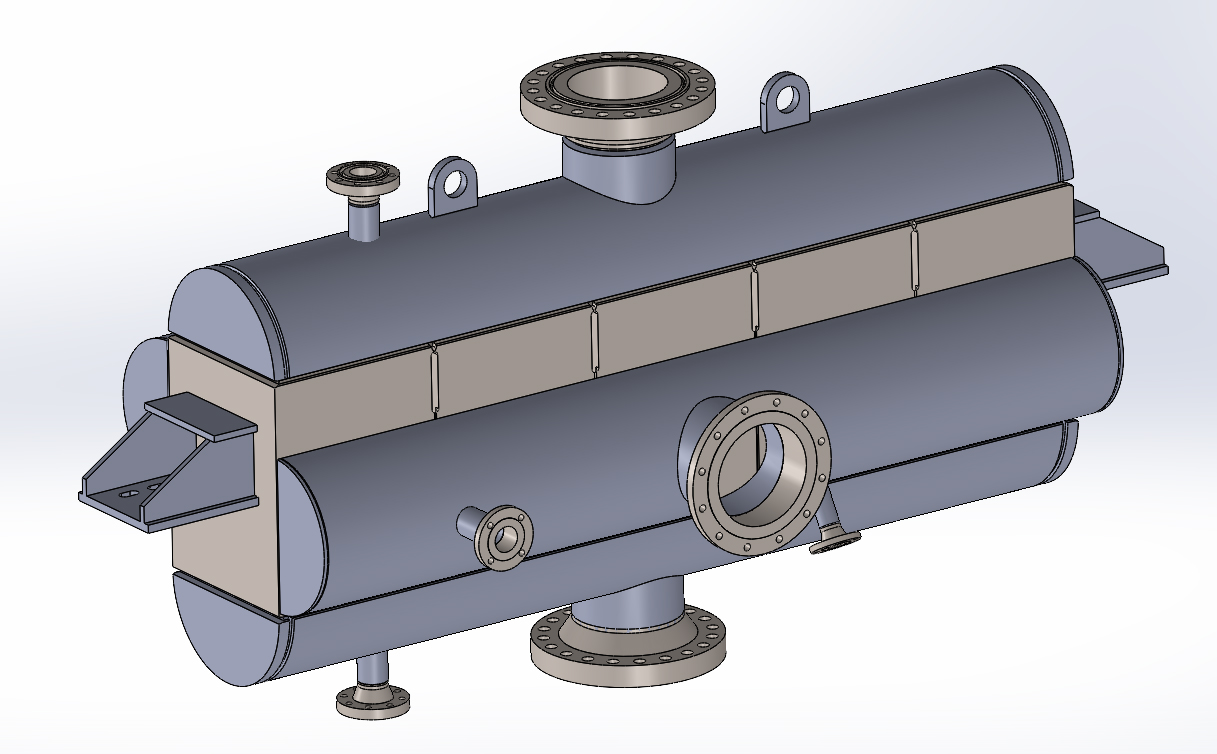
Rendering of the large PCHE heat exchanger for an oil & gas offshore plant
MCD is therefore working to create its first PCHE exchanger for an offshore Oil & Gas plant, which will be over 3 meters long and weigh more than 8.000 kg. The exchanger will be made up of 5 blocks of photo-etched plates, welded using diffusion bonding technology with welding seams of specific geometry, specifically designed to allow 100% control using gamma rays.
The sizing of the exchanger was supported by thermo-fluid dynamic tests on dedicated specimens. The acceptance tests will involve the ability to test a vessel capable of containing hundreds of liters of gas or water, and of managing flow rates of 200.000 litres/hour. The machining and metal-working systems that MCD acquired in 2024 proved to be perfectly suited to the order, including a cutting machine and a five-axis machining center for the mechanical processing of the blocks, both capable of working large dimension components, and a second chemical etching line which in six weeks will allow to create all of the 2.600 channeled plates necessary for the construction of the exchanger.